- LEED v4 Platinum Certification
- Targeted to be Net Zero energy operations (EUI of 0 vs. a standard building EUI of 65)
- Top 1% of building performance nationally, measured by Energy Use Intensity (EUI)
- Embodied carbon reductions in line with UA 2050 net zero goals
- WELL Building Standard
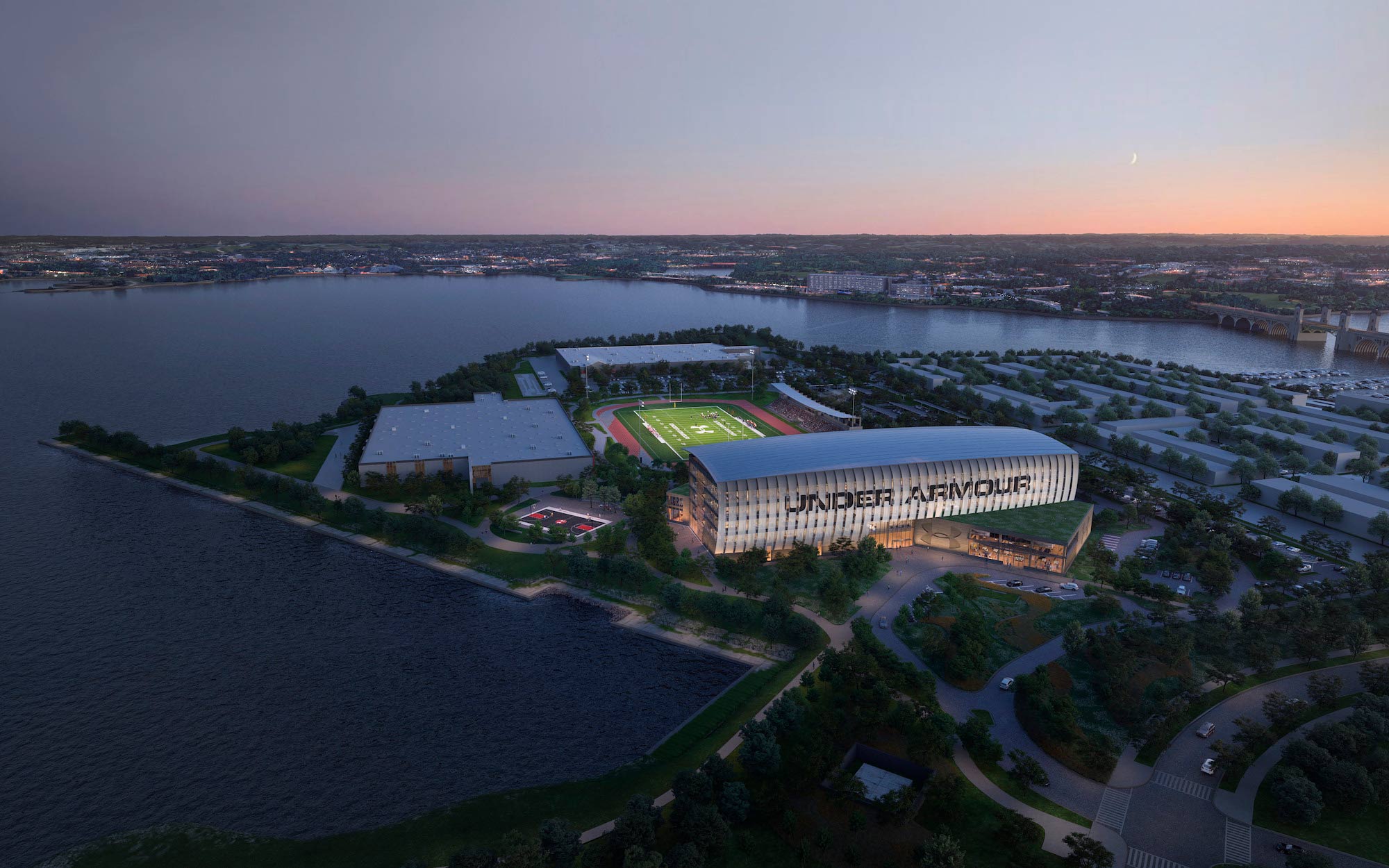
Under Armour’s sustainability goals are ambitious. In addition to advancing circular economy, global take-back programs, and using recycled materials in apparel and accessories, the company has committed to transitioning all of its owned and operated facilities to 100% renewable sources by 2030, and to reach net zero greenhouse gas emissions by 2050. As these commitments crystallized, the company also embarked on the creation of a new global headquarters to better support its teammates and its net zero mission.
For Gensler, the challenge at hand involved determining how Under Armour’s real estate should evolve to enable the company to meet those goals, with the new headquarters serving as a North Star for its key value of “Act Sustainably.” To create a sustainable campus at this scale, we had to take multiple design resilience approaches — from material selection to energy planning to interior health and well-being strategies — intertwined across the campus with visual expressions of the Under Armour identity and brand.
Gensler, in partnership with Interface Engineering, took on the initial task of charting the project’s path to net zero energy operations. The design team, consisting of a combination of architects, interior designers, and sustainability experts, outlined a strategy to reduce the project’s EUI (Energy Use Intensity) from the industry baseline to zero. This involved reducing the amount of energy the project would use, reclaiming local resources, and creating on-site systems to generate and save energy — in essence managing a carbon balance sheet for the project balancing material and operational impacts.
Within the context of this reset energy balance sheet, the project sets the stage for its sustainable design solutions to take on beautiful forms. A visitor may not know the intricacies of how the building treads so softly with respect to the local environment, but they will immediately grasp what Under Armour believes in.
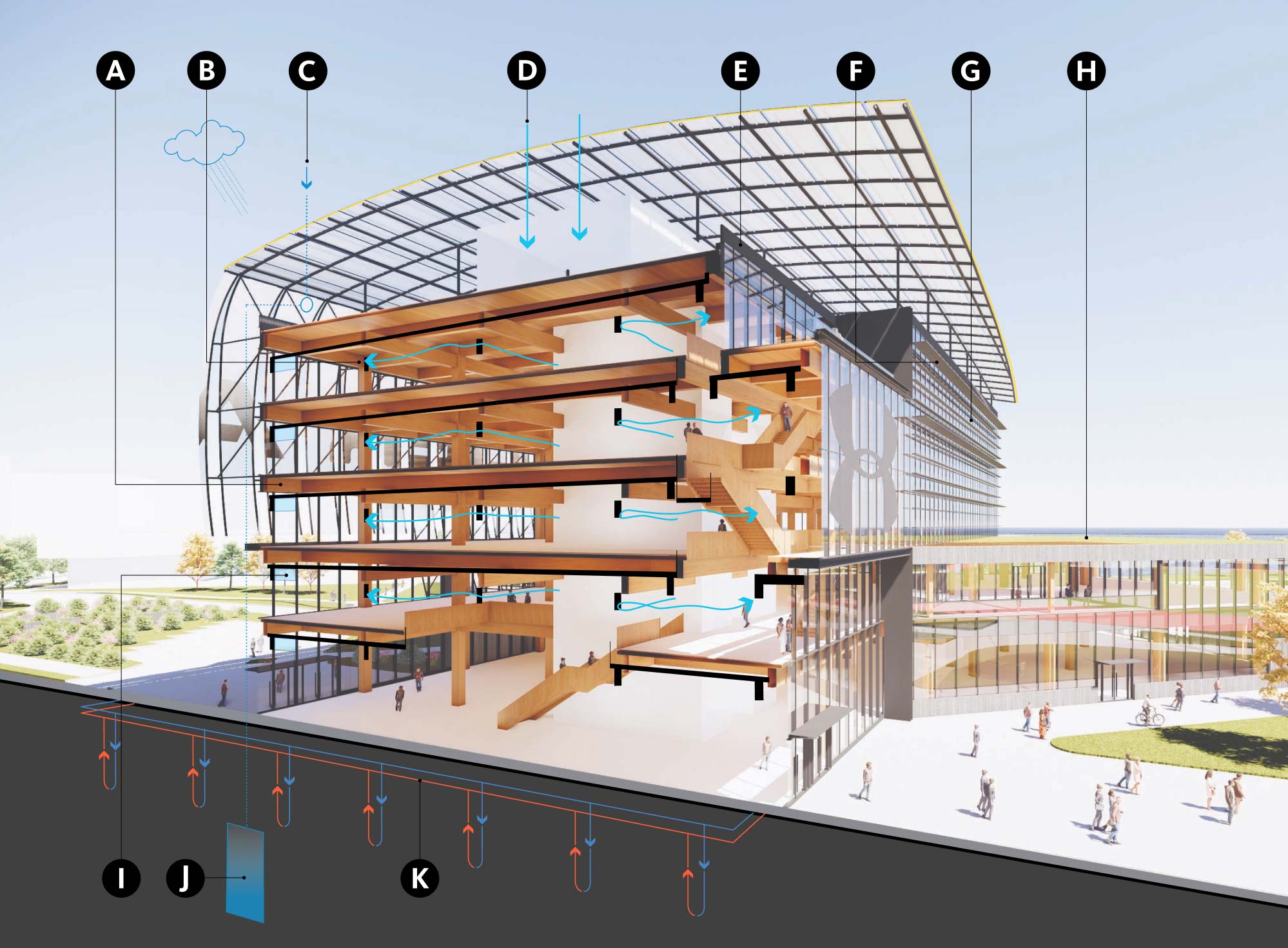
MASS TIMBER
With an eye toward its 2050 goal of achieving net zero greenhouse gas emissions, Under Armour decided to use mass timber instead of steel to lower the project’s embodied carbon. The chosen structural material served as a baseline that would elevate the impact of many of the building’s other sustainable design features. To pursue mass timber explorations, Gensler partnered with structural engineer Thornton Tomasetti and brought a manufacturer on board to ensure a smooth process. Supporting Under Armour’s decision to pursue a mass timber building was how well the material aligned with the athletic apparel and footwear company’s brand, which revolves around authenticity.
GEOTHERMAL HEATING AND COOLING
While the PV panels are on center stage, other sustainable design elements are hard at work underground. The main building uses geothermal heating and cooling systems to keep day-to-day operations on-campus comfortable, significantly reducing its energy footprint and capitalizing on both state and federal incentives available for using the strategy. Additionally, the HVAC system, with enhanced filtration and indoor air quality monitoring, boasts 100% energy recovery.
PHOTOVOLTAIC PANELING
Since their invention, photovoltaic panels (used to generate energy from the sun) have had a significant drawback: their appearance. As the technology developed however, these panels have become slimmer, with increased power output capabilities. Our project team took advantage of newer, nimbler panels to incorporate the photovoltaic array into a curved canopy structure. With elegant bends and twists, the array becomes an ode to the idea of performance itself, both in terms of form and function.
RAINWATER HARVESTING
The photovoltaic system joins forces with a series of strategically placed sunshades to reduce the building’s energy usage (studied and modeled in partnership with Interface Engineering), and even aids with rainwater harvesting to support the surrounding landscapes. Enough rainwater is expected to fall on the roof annually to meet 100% of the project’s flushing water needs — a high percentage of its water consumption. The system also helps to protect local waterways by reducing the pressure on the storm drainage infrastructure.
BIOPHILIA
Whereas traditional designs call for concrete columns that are subsequently covered in drywall and then painted, mass timber designs like Under Armour tend to expose the structure and embrace the material’s natural beauty and wood tones. As companies increasingly focus on enhancing employee well-being via workplace design, mass timber’s utility and quality will only increase its value. Educational moments are sprinkled throughout the exterior landscape, illuminating the area’s natural character as well as the community’s story. The landscape design prioritizes the campus’s walkability, with pedestrian connections set within the bioretention plantings. Providing employees with easy, everyday access to green space and natural light was key to the project’s pursuit of the WELL Building Standard.
HIGH-PERFORMANCE LANDSCAPE DESIGN
For Under Armour, it was critical for the project’s sustainable and resilient mindset to extend beyond its four walls. Because the site had been an industrial shipping yard for more than 100 years, its original contours became flattened, and native species crowded out. Seeking to reclaim Port Covington’s natural landscape, the Gensler team, along with its landscape architect partner Nelson Byrd Woltz, has introduced berms, bioswales, and rain gardens for on-site stormwater management. The selected plantings, including grasses, perennials, and woodlands, are native to the area, ushering in a long overdue recalibration. To shore up the project against anticipated sea level rise, the main building itself is elevated 17 feet.
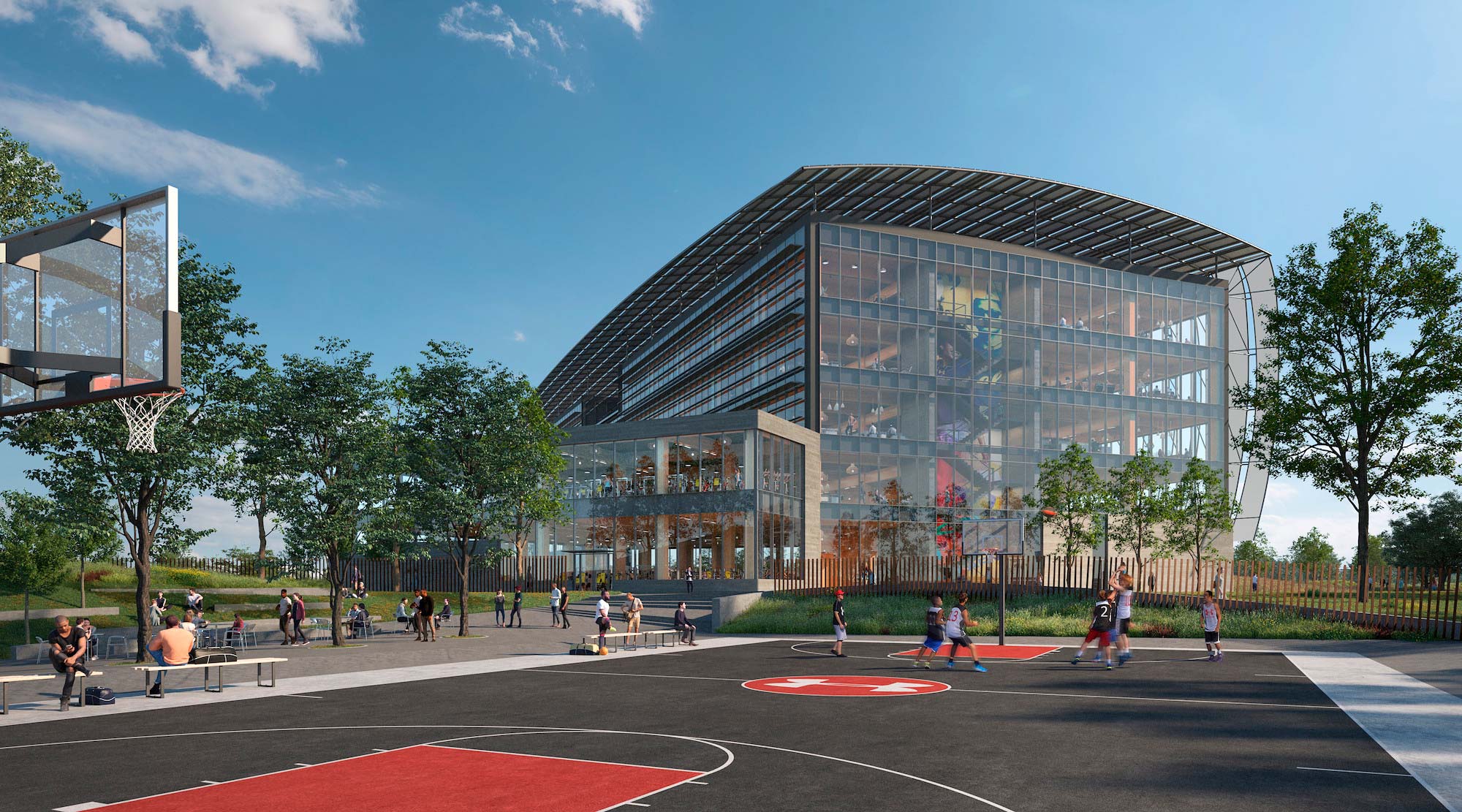
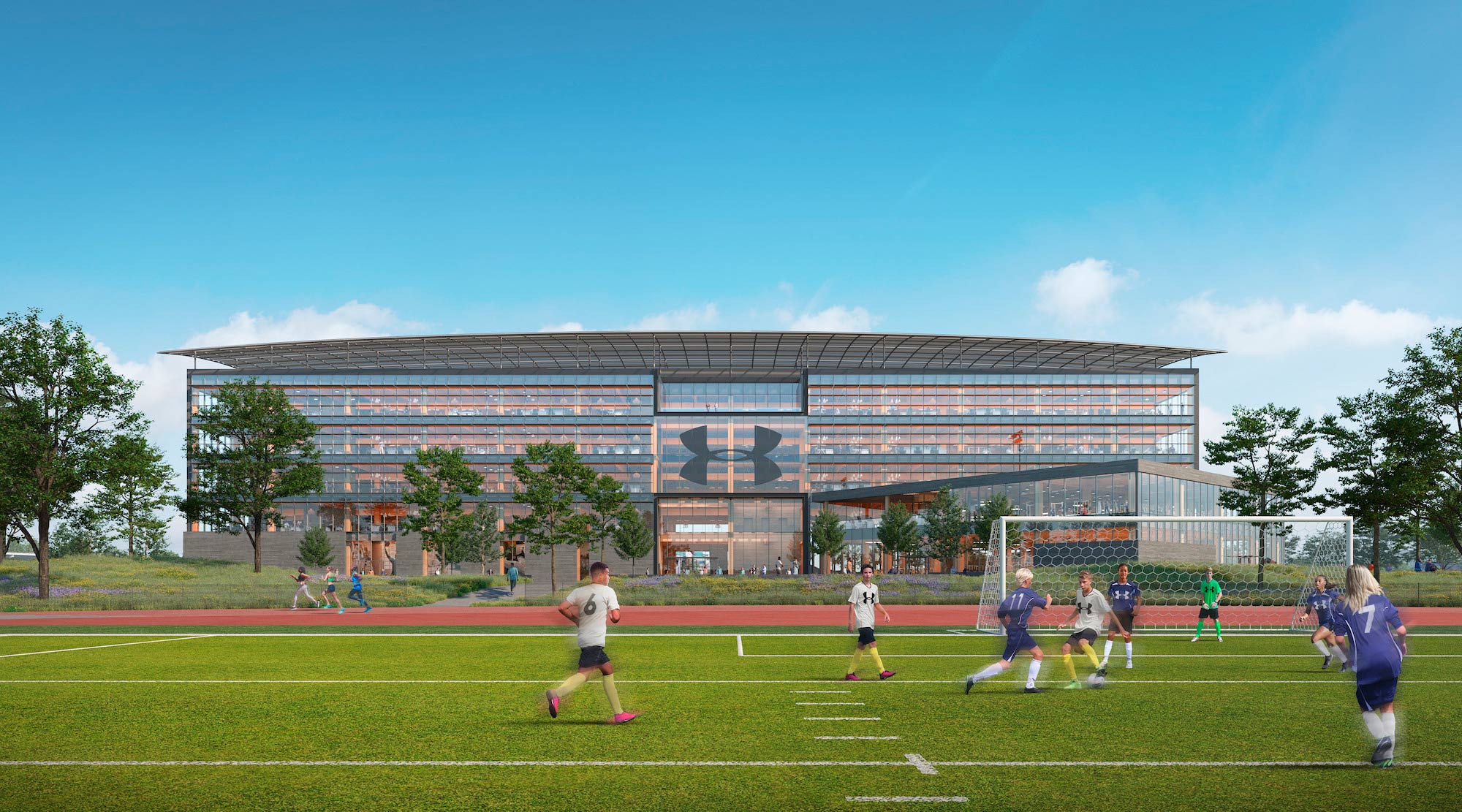
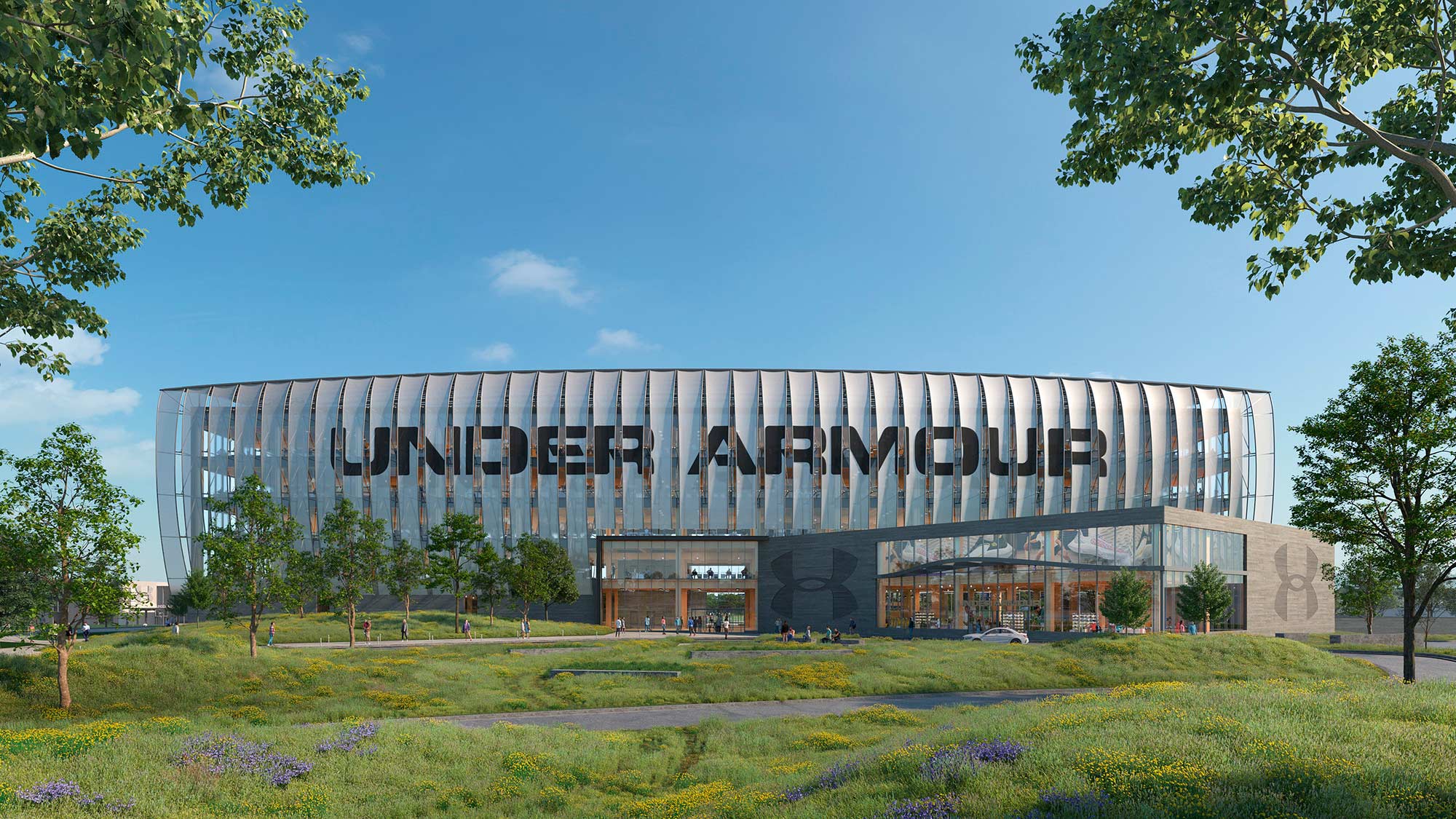
-
The Baltimore Sun shared that Under Armour will kick off the move to its new global headquarters ahead of schedule. Gensler Principal JJ Rivers said the mass timber structural system “sets a new standard” for a truly sustainable corporate campus.
-
Reboot Chronicles featured a podcast with Gensler’s Jordan Goldstein and Julia Simet. They shared insights on how they are redesigning the future of work through physical and digital environments and how spaces should adapt to our evolving needs.
-
Daily Commercial News spotlighted Gensler’s unique design of Under Armour’s global headquarters, which stands out for its form — a sports stadium-like space — and for its sustainable mass timber structure.
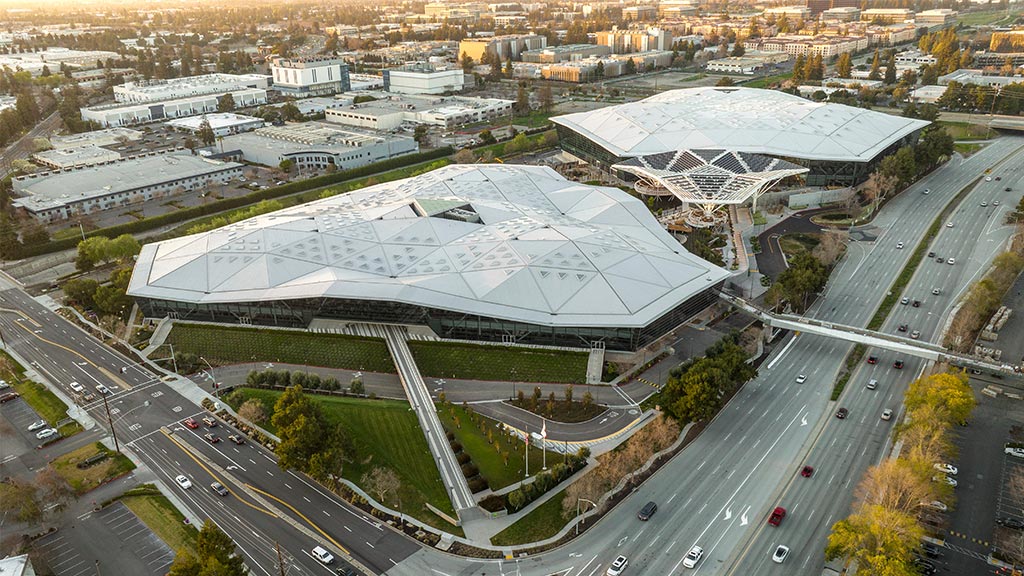
NVIDIA
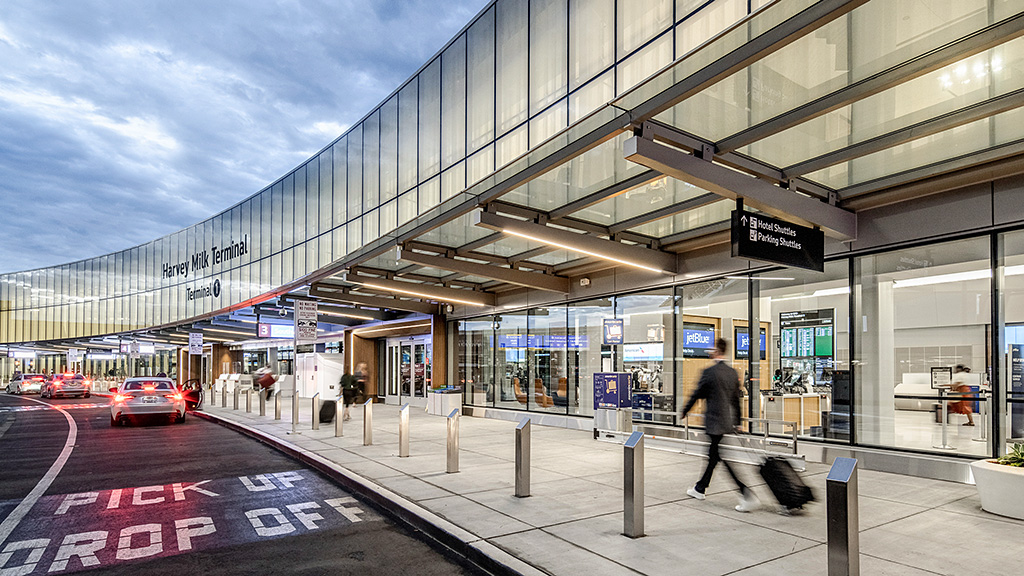
San Francisco International Airport, T1 Net Zero Program
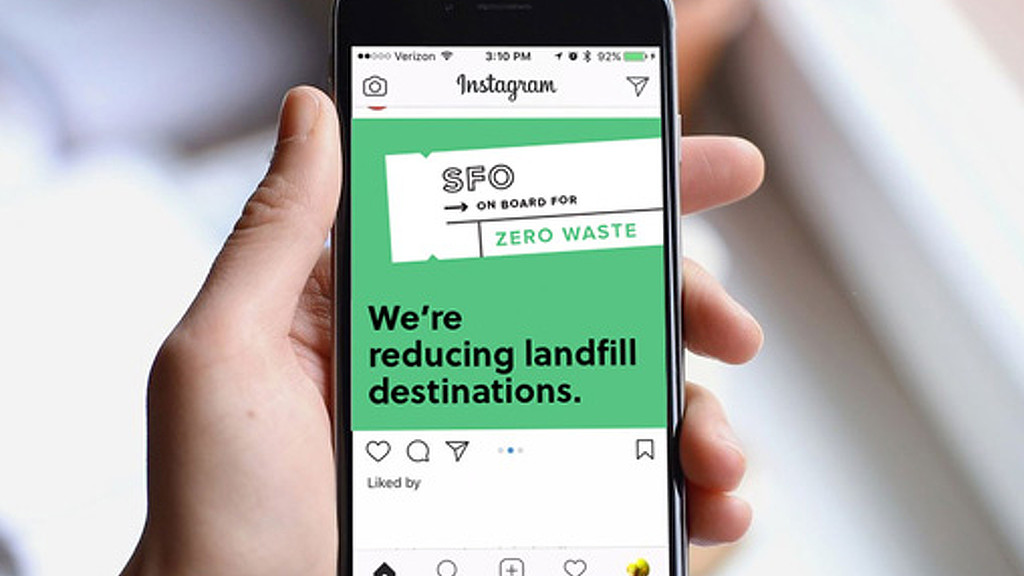
SFO Sustainability Campaign
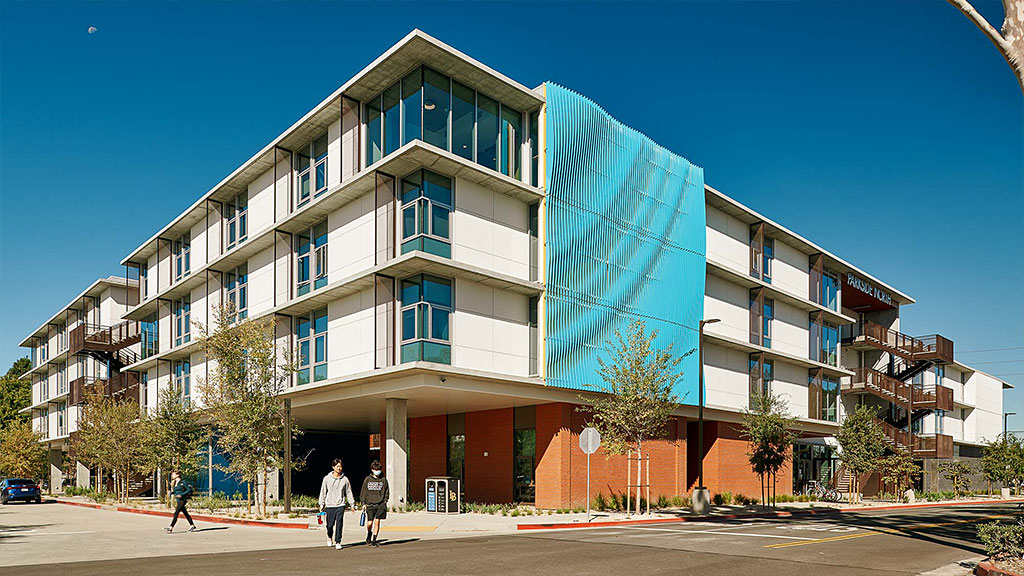
CSULB Parkside North Residence Hall and Housing Administration Building
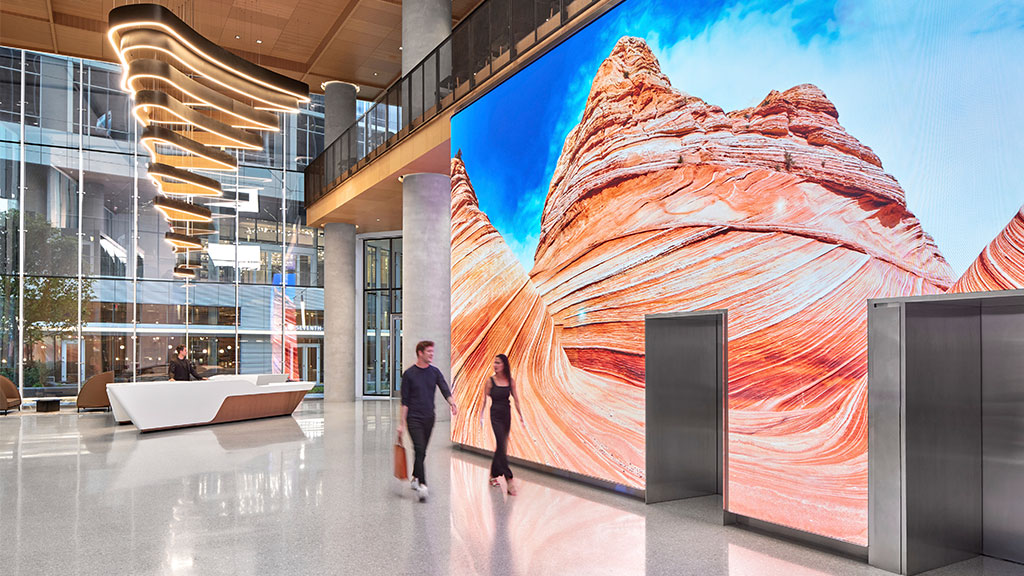
Marriott International Global Headquarters
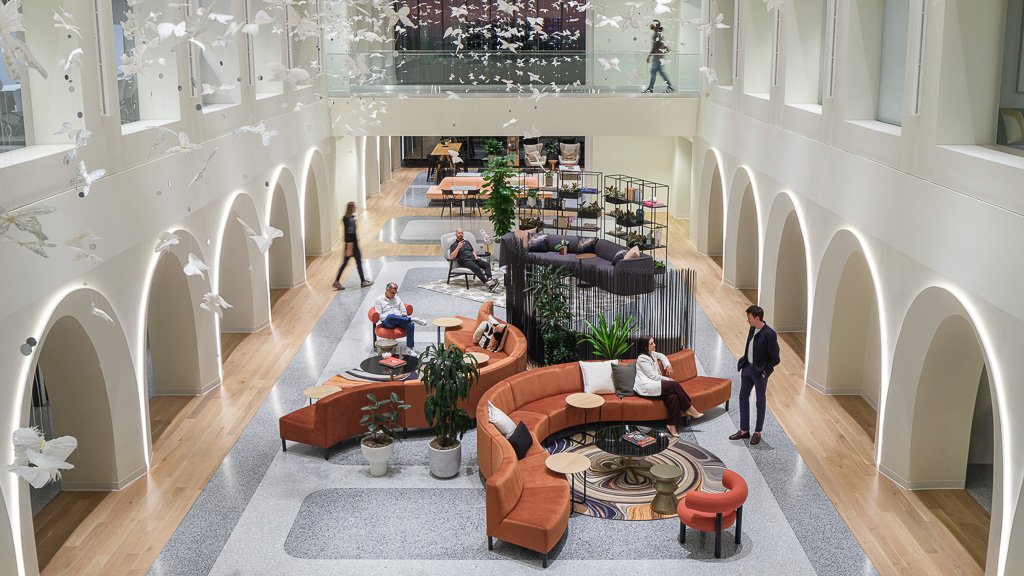
Neiman Marcus Group Dallas Hub
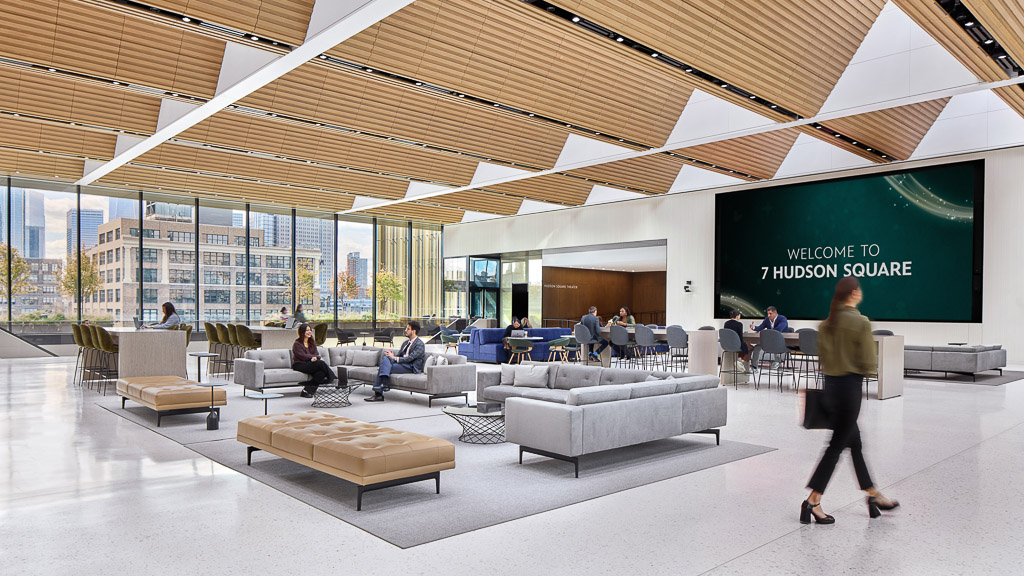
The Walt Disney Company NYC Headquarters
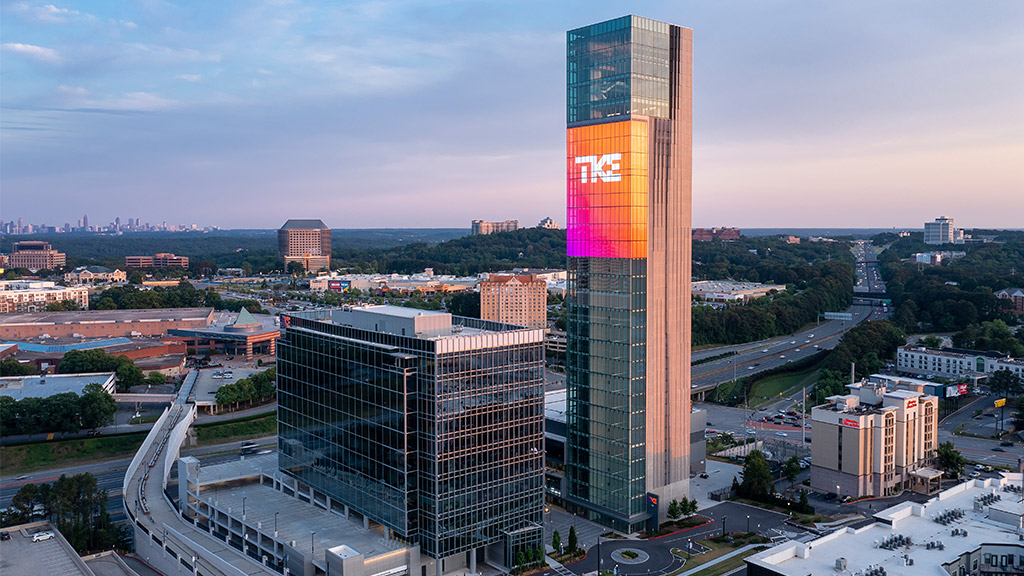
TK Elevator North America Regional Business Support Center
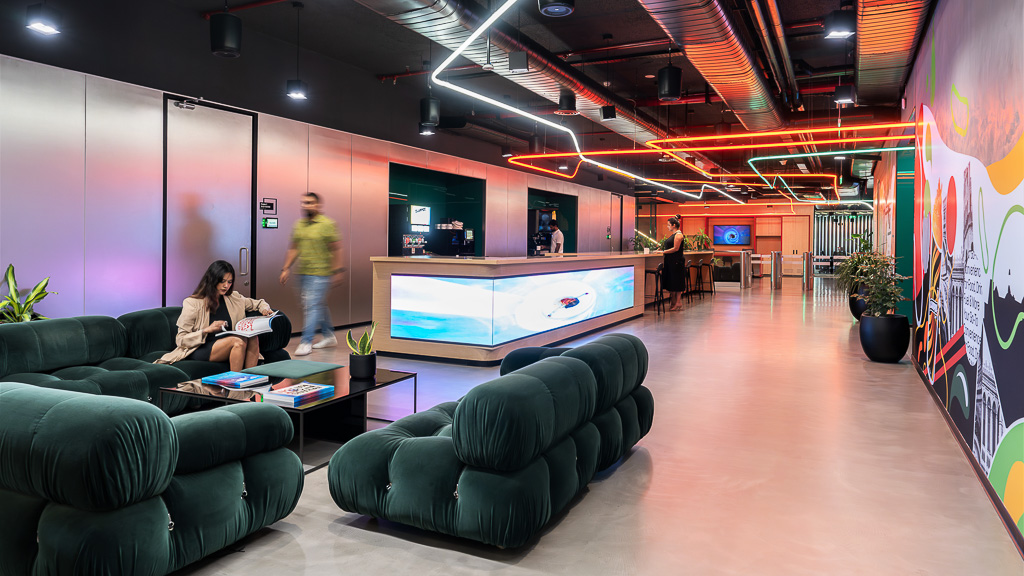
7-Eleven Global Solution Centre
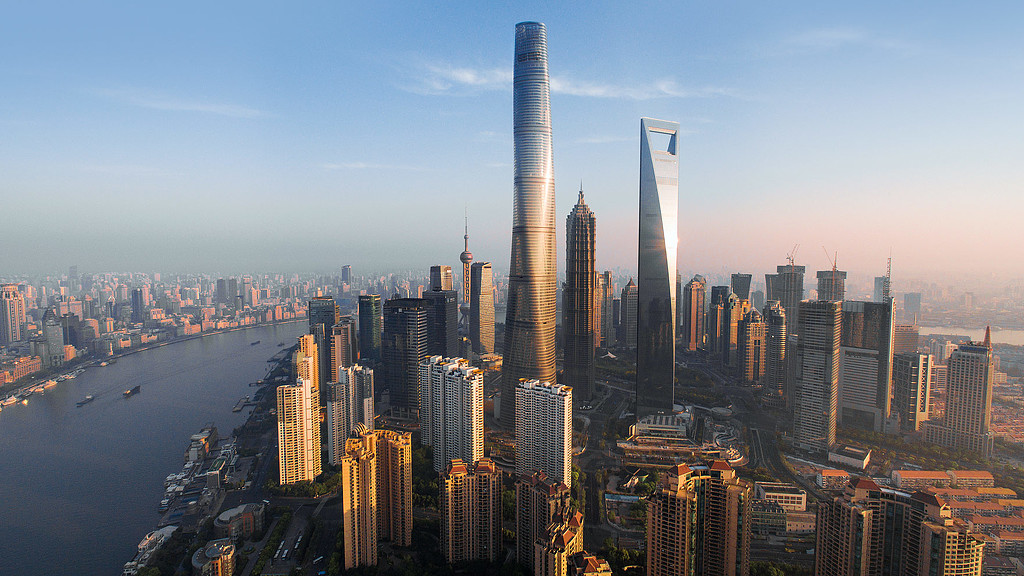
Shanghai Tower
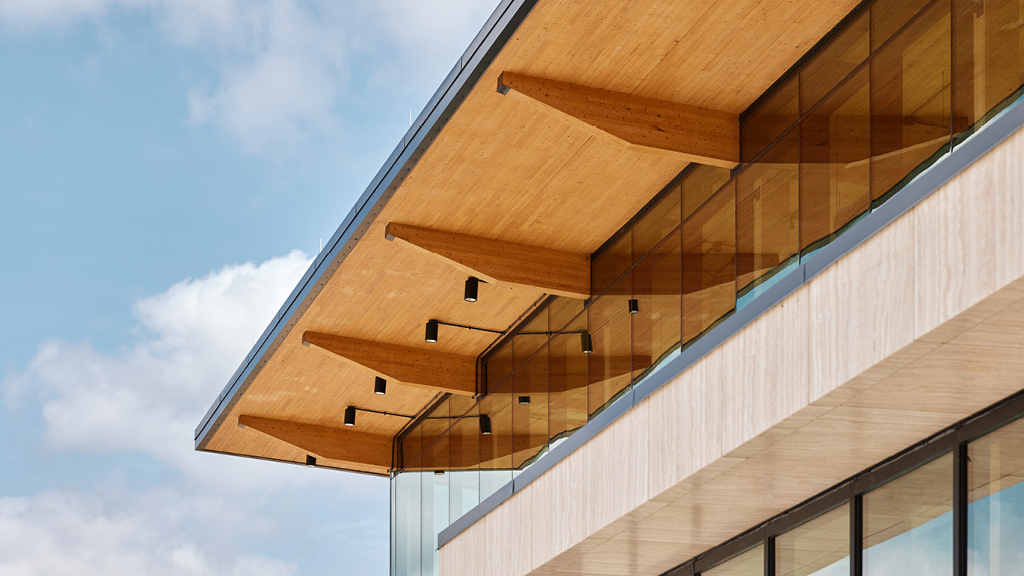
Climate Action Through Design
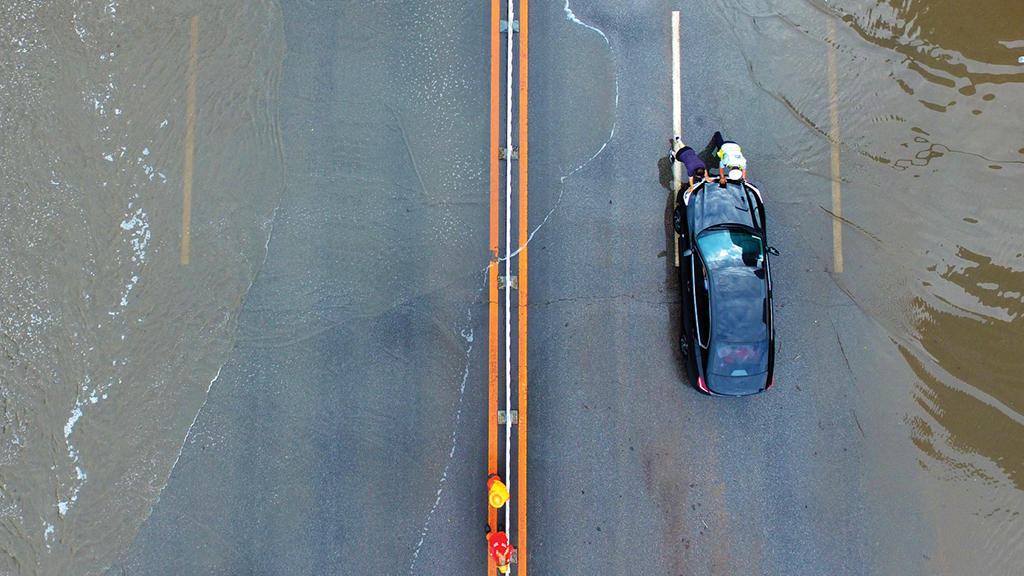
Global Climate Action Survey 2024
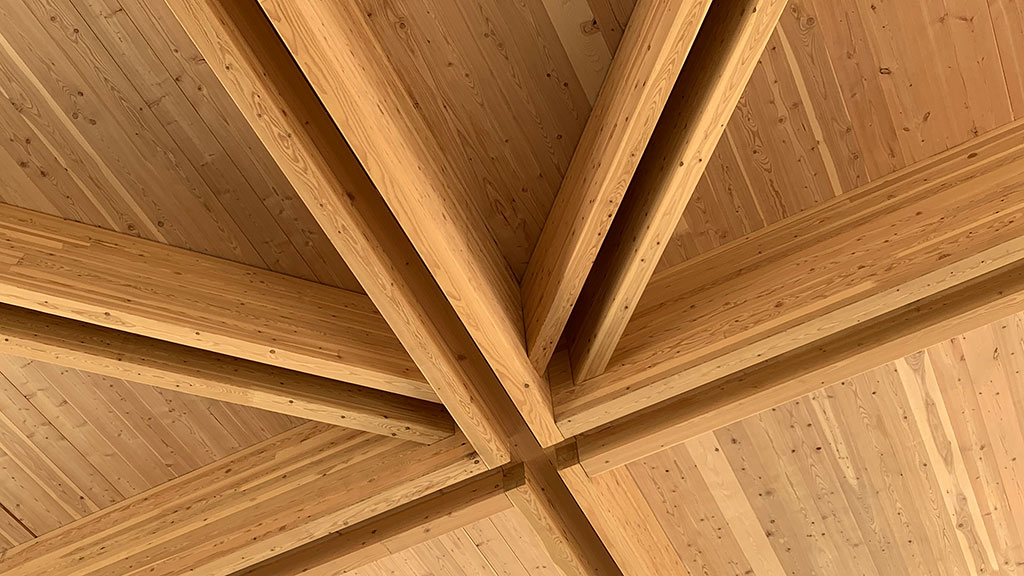
5 Things Developers Should Know About Mass Timber
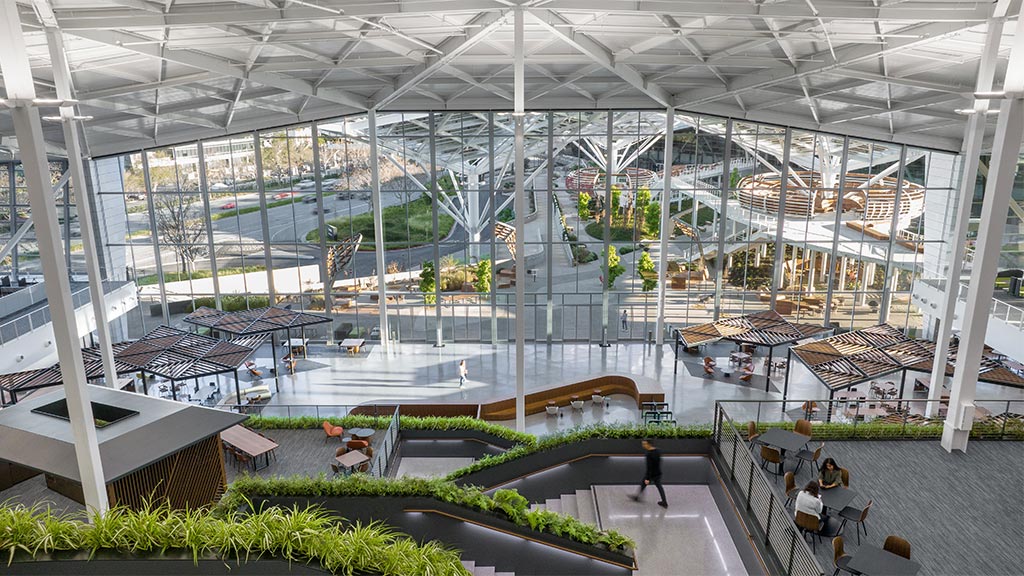
The Definitive Value of Build to Suit: Building Purpose From the Ground Up
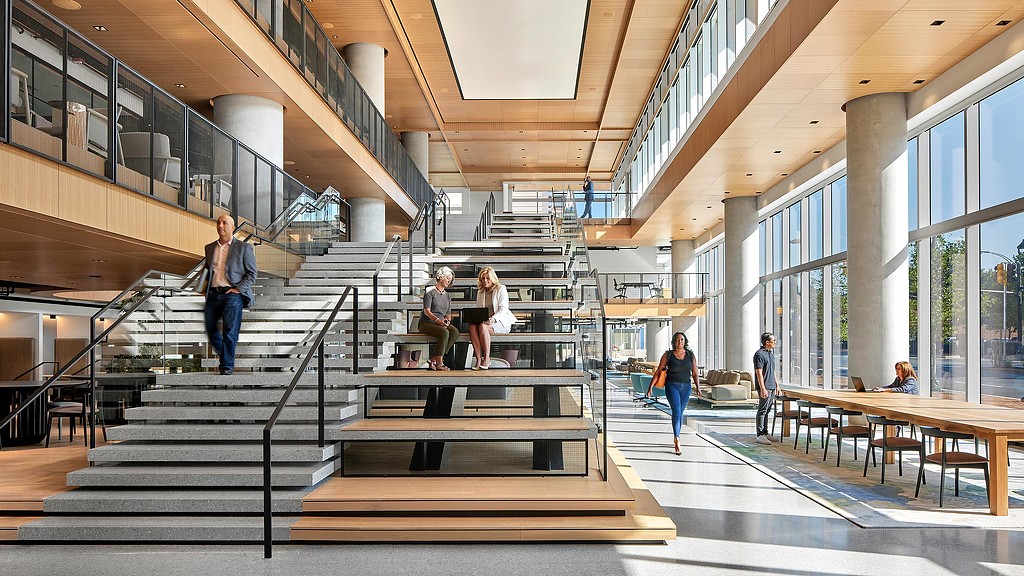
A Material Approach to Lowering Carbon and Changing the Building Industry
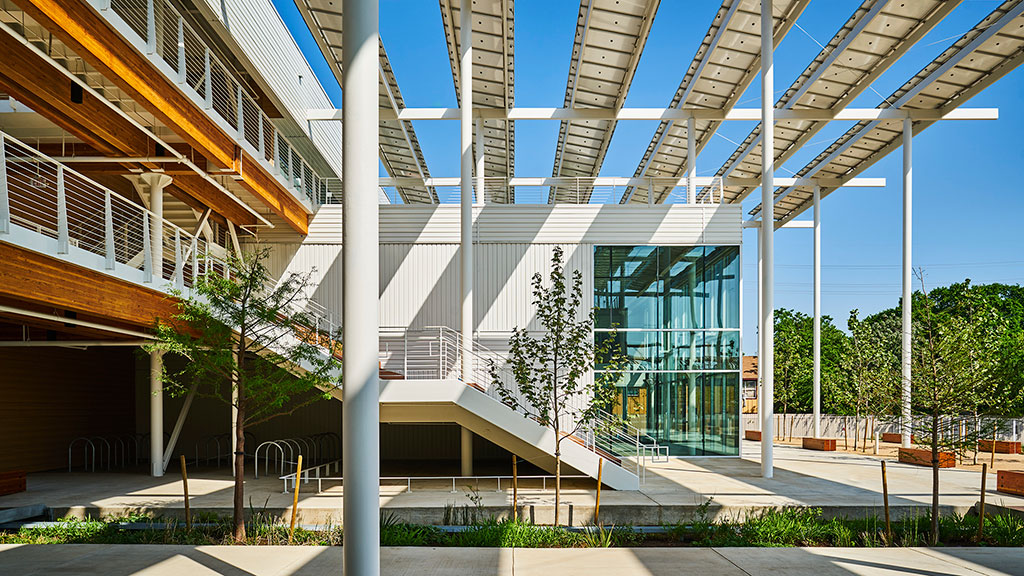
Back to Basics: 5 Strategies to Approach Net Zero Energy
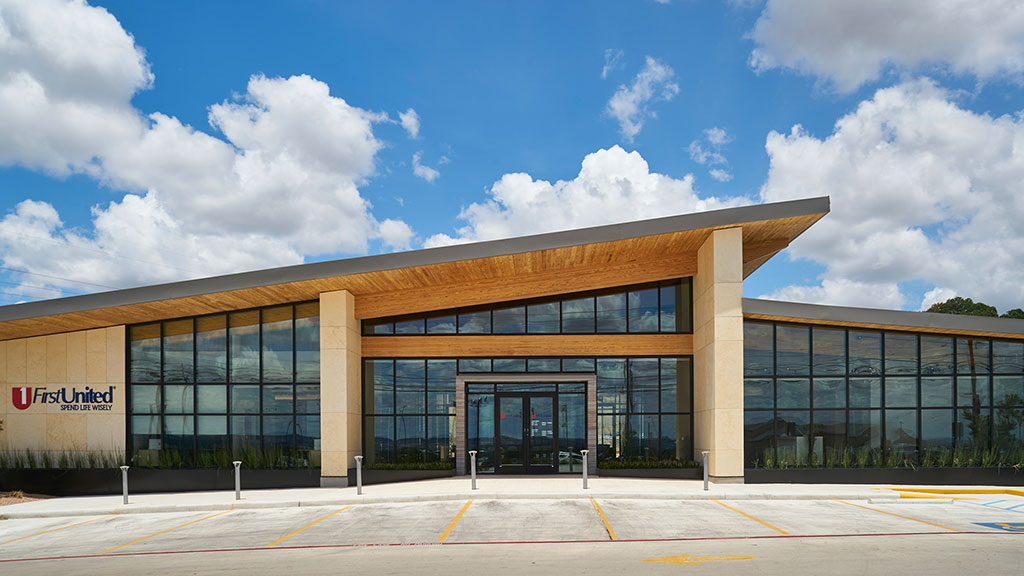
Mass Timber: The Sustainable Solution for the Design Industry
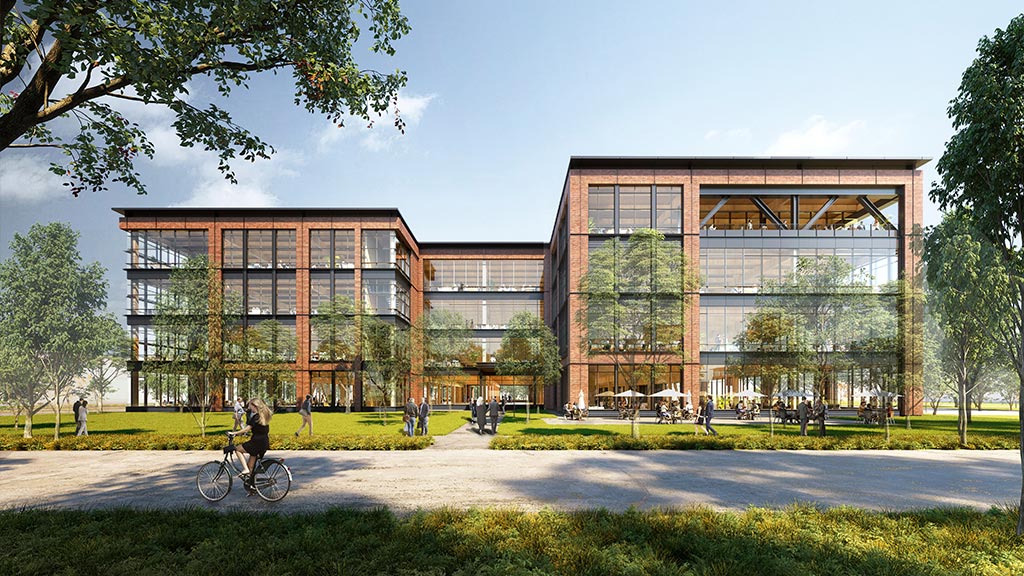
Mass Timber: The Sustainable Solution for the Design Industry
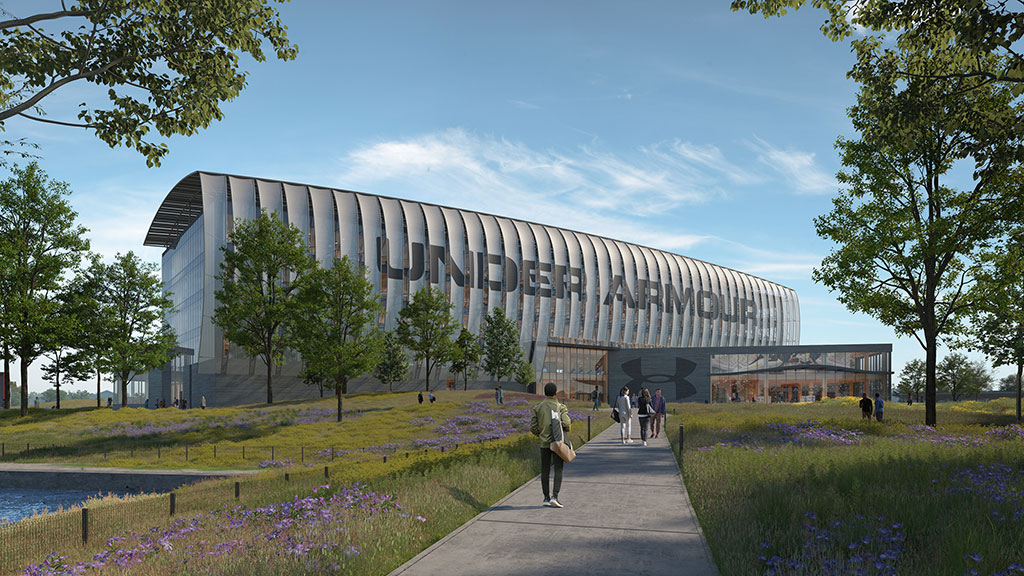
Is Mass Timber the American South’s Best Kept Secret? Not for Long.
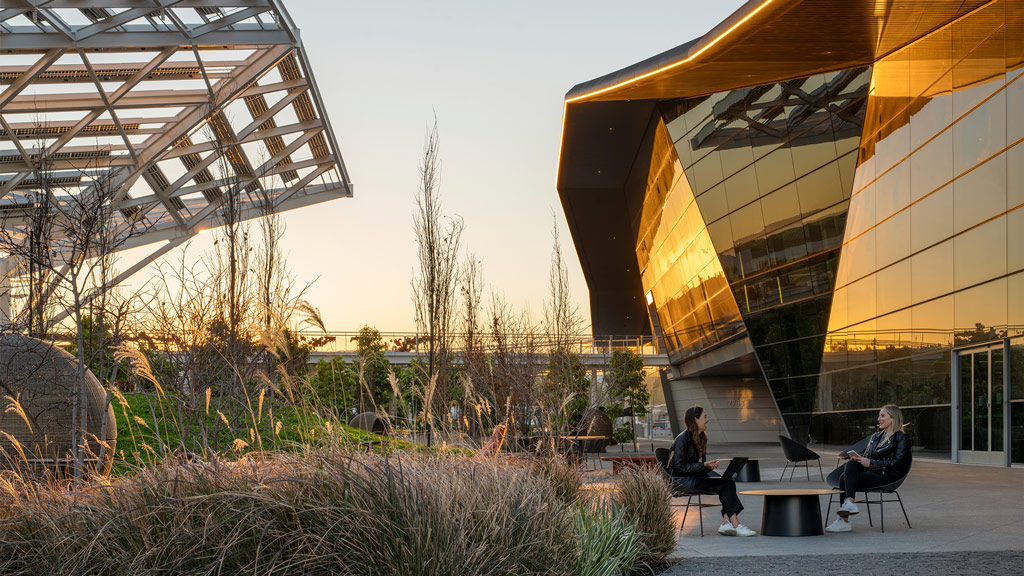
5 Ways ESG Can Influence Design and Create Opportunities
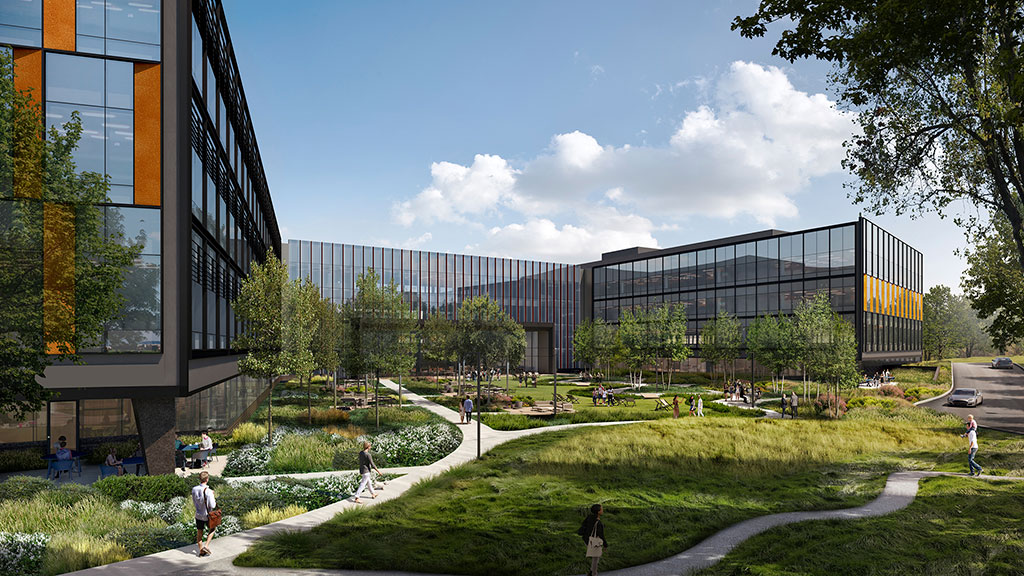
Preparing for a Resilient Future Through Climate Action
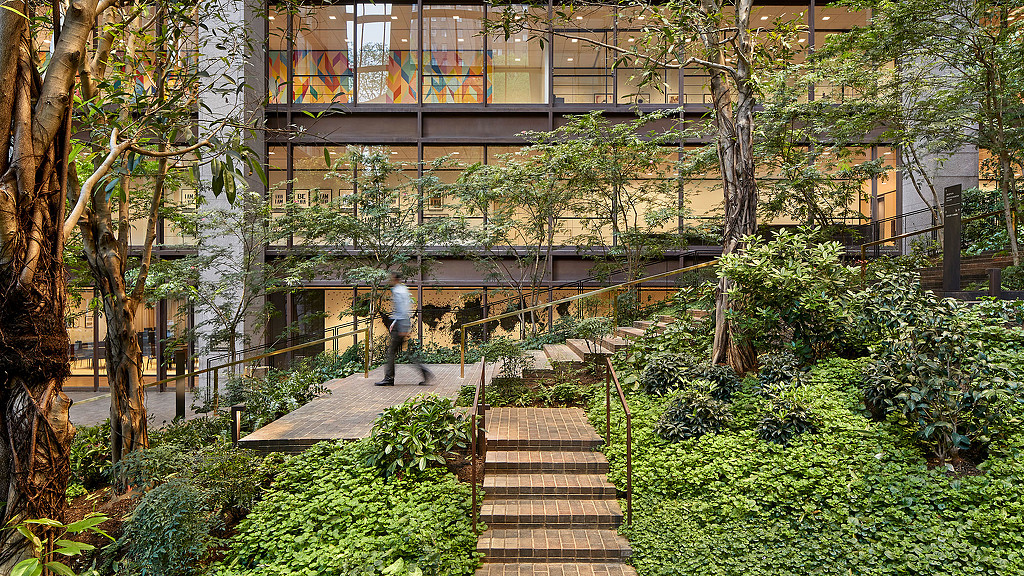